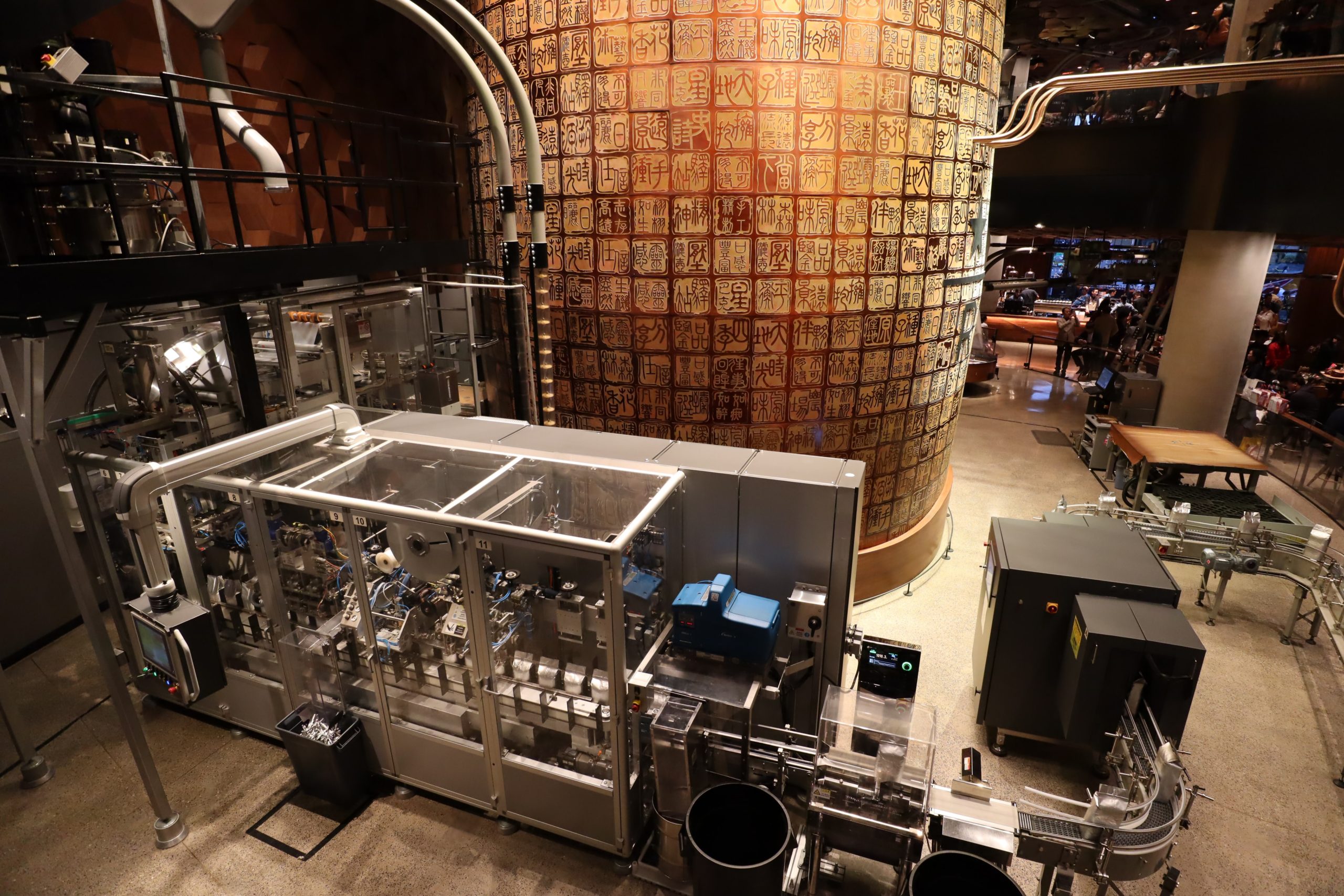
Manufacture fit for a modern workforce
Workers are the biggest assets in the evolving manufacturing industry. Today’s employees expect up to date work environments, managed differently than they were in the era that began at the start of the 1900s. Industry therefore must find a way create a workplace fit for the digital age.
Manufacturers have heavily invested in transforming their operational technology (OT), creating more connected and intelligent factories, equipment and supply chains for big gains in productivity and new ways of doing business and making money.
For the employee however, the industry’s IT investment hasn’t kept up. Its workforce still faces many of the same challenges it has for the past decades, meaning that there is untapped productivity yet to be realised and tapped into with up to date processes. Today’s industrial environment requires different skills for factory workers, i.e. how to configure and service robots in order to work with them and in ever evolving ways.
For the likes of firstline workers like plant floor operators, field service technicians and delivery specialists, the need for innovation is pressing. Manufacturing employees make up a massive segment of the industry’s workforce, yet Forbes Insights found that only 36 percent of firstline workers have the technology tools they need. In manufacturing, the majority are forced to spend significant amounts of time searching for information in the field, are unable to collaborate with experts, use digital resources and are bogged down with manual outdated process.
IT transformation is important for information workers, such as product engineers and plant managers, who need the efficiency gains made possible by new analytics, design and collaboration tools. Compounded by the expectations of digitally-savvy millennials entering the workforce, and a new and modern way of working becomes critical to the manufacturing industry’s success.
How can today’s technology innovations help?
There are many examples of manufacturing leaders tapping into the latest digital advancements to achieve a modern manufacturing workplace and its benefits. Aston Martin is a great example, firmly on track to accelerate production by using Microsoft 365 digital tools to energise employee creativity, data insights, and teamwork.
The building blocks of a modern manufacturing workplace
Today’s digital advancements offer tremendous opportunities to transform the manufacturing workplace—enabling IT to catch up with OT. Innovations like world-class mobility, cloud, IoT, advanced analytics, AI, wearables, and mixed reality devices, can be used and combined to provide powerful productivity and collaboration-enhancing capabilities for first line workers and information workers, and throughout teams and the manufacturing enterprise and supply chains.
Mixed reality technology, in particular, offers an unparalleled opportunity to transform how employees interact with their environment and collaborate in problem-solving—from engineering to manufacturing, field service and training.
Building a modern manufacturing workplace also sets the foundation for a more efficient manufacturing operation by bringing together smart connected things, the intelligent cloud and streamlined people processes. Let’s look at a few examples.
Empowering employees for success
A modern manufacturing workplace enables workers across four key manufacturing functions:
- Operations. By investing in the right tools manufacturers can improve efficiency across all areas. They can automate core processes and augment employee work by taking advantage of new advances in human-robot collaboration to maximise employees’ time. They can enable efficient problem-solving and issue resolution through sophisticated knowledge management, collaboration and communication. And they can distribute training to any device and bring new employees up to speed. Additionally, mixed reality facilitates employee training. Virtual scenarios can simulate common problems that employees will encounter on the job to better prepare them for troubleshooting.
- Services. Technicians are equipped with the tools they need to improve services and encourage customer engagement. Mixed and virtual reality can prepare technicians prior to a service call better than before with all information required to successfully complete their task—and do it hands-free. It also facilitates remote collaboration with an expert in order to maximise employee expertise.
- Plant management. Manufacturers can help their managers to pin point insights and enhance productivity. This can include simplifying scheduling and staff management to allow seamless shift changes and eliminate production bottle necks. With new levels of visibility, intelligence reports on equipment efficiency, it helps plant managers to spot production problems faster and enables employees to be productive, all while protecting priceless IP and customer data.
- Product engineering. With better resources for design and collaboration, manufacturers can harness the creativity and innovative power of their engineers. By analysing data from connected products, engineers can more easily develop customer-centric designs. Collaboration tools allow engineers to work together in a seamless environment, co-author designs, and share documents securely. Mixed reality is also unleashing creativity through the visualisation of design concepts. Rather than needing to physically produce prototypes, designers can iterate digitally and see the impact that different ideas would have on a product. This reduces the amount of time for design iterations and makes it easier to test out creative ideas.