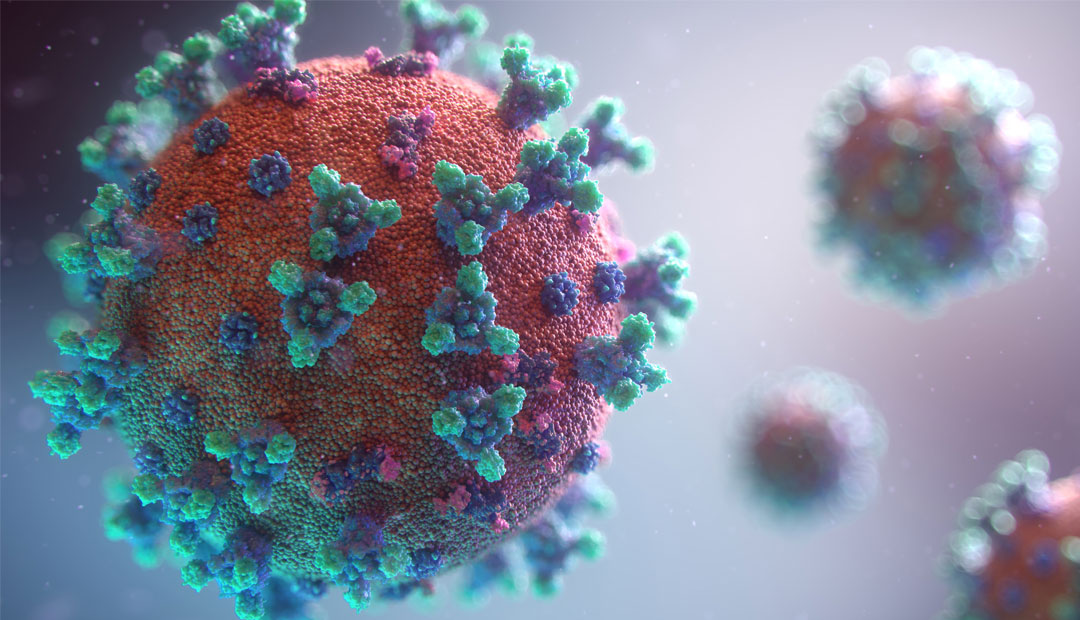
07
May
One Point Zero Newsletter – How to Order PPE, Regulation Changes and Misinformation
Another week has passed, and the implications of governmental changes has had a large impact on shipments of PPE, causing delays and frustrations amongst both buyers and suppliers. We have compiled the key points below to try and explain the global situation and provide some insight as to how to get around the problems that most are currently experiencing.
How to Order PPE
With the press hounding the public with stories of how government bodies should be doing more to bring in PPE, it can be difficult for people to truly understand what goes into purchasing masks, gloves and other essential protective equipment.
It is difficult for buyers who are not used to having to deal with such demand within such a short timeframe. It is even more confusing for the purchasers who previously have had no direct experience in liaising with Asia. With supplies dwindling, companies and organisations such as hospitals, fire services and union workers are now trying to navigate the minefield of doing business in China, which is sadly leading to a lot of orders and not necessarily a lot of supply.
There are several things to be aware of when establishing a partnership with a management team or manufacturer in China.
-
Firstly, regulations and certifications are key. Without them there is no continuity and no guarantee that what is being ordered is what is being delivered. Find out more here.
-
Secondly, there is a process. A list of requirements that are essential for successful delivery of quality product. We covered this in our previous newsletter, however already this list is out of date due to new regulations being brought in. It is important to remember that the process is continually changing, and new requirements are being regularly brought in, sometimes overnight.
-
Finally, do not try and do it on your own. If you are new to purchasing PPE (even if you have previously done business in China for a non-related product) use an organization or company that has proof of distribution in PPE within the last month. With the ever-changing climate in Asia and the number of hoops there are to jump through, it is crucial to work with a supply chain partner who can navigate this on your behalf.
Distribution Limitations
There are 3 main ways product is shipped out of China and onto its destination and depending on what the product is, it will depend on how it can feasibly be transported:
Air freight – this is for light items with a turnaround time of 8-10 days. With flights out of China highly sought after, this is mainly being used for masks and respirators.
By Rail – this is for heavy and bulky products such as gowns and gloves. Much slower, this can take 25-30 days.
By Boat – by far the longest method of transport this is reserved for the largest items that cannot be moved any other way.
Import Tax in the EU
The EU has agreed to waive import and customs tax on Personal Protective Equipment (PPE) and other medical equipment including ventilators and testing kits. However, it is up to the individual countries of the EU to state how they will enforce this. For example, France has stated that any company can import up to 5 million units of PPE into the country without any import tax. Unfortunately, it is unclear as to what this means. Is it 5 million of one type of product or is it 5 million total across the PPE sector?
Clarity is key for distribution. If interpreted incorrectly, shipments will likely be seized at customs and never reach their intended destination. Instead governments may use the seized shipments for their own use and be distributed to hospitals of their choosing.
Misinformation on Customs Seizures and Product Specifications
It is easy to panic when a news cycle picks up a certain topic and suddenly it’s everywhere. One such topic this week has been the seizing of masks by customs. This is scaring buyers into being reluctant to commit to orders with the worry that they would spend a lot of money and never receive what they paid for.
This has been grossly exaggerated. A very small percentage of shipments have been seized, mainly due to not meeting standards or regulations required by customs. A far greater percentage of shipments are successfully passing through customs and buyers must not be put off by these headlines.
A lot of specification information on individual items, especially masks are incorrect. Not only should this be a red flag, but it also highlights the importance of knowing what you are looking for. As discussed in last week’s newsletter, the standards that masks are supposed to be made to is essential to get right, otherwise the masks are likely ineffective in stopping the spread of COVID19.
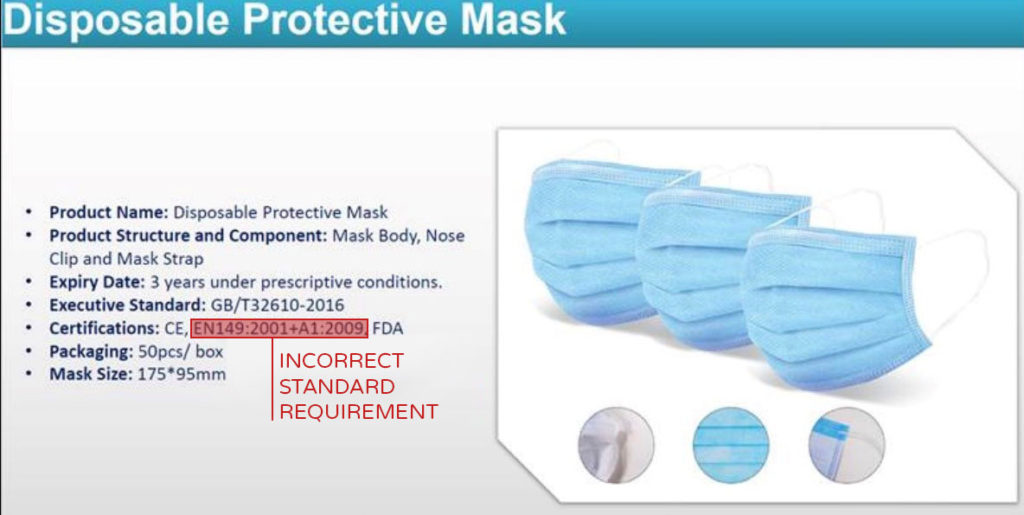
Why Countries Are Turning to Their Own Vendors for PPE and Why This is a Mistake
To combat mask shortages and long waits for shipment arrival, some governments are turning to their own national manufacturers to produce the necessary protection. This is due to customs changes and the difficulty in importing product across EU borders. These factories are likely to have been transformed from textile to mask only production lines. In both France and Germany, there are online government portals, listing all the national vendors of alternative masks.
Whilst these efforts are helpful in easing the burden on supplies, these fabric masks are not made with a filtration material and do not meet the standards that have been stated as required by the World Health Organisation to prevent the spread of COVID19. These fabric masks unfortunately perform drastically worse than the standard EN14683 masks and do not provide an adequate level of protection as published in a report by the ECDC in March 2020 which can be found here.
The only mask that is recommended by healthcare professionals are the N95 and FFP2 (EN149 certified) masks as they have the necessary filtration to stop the movement of the COVID19 virus particles and the general population should pay attention to using medical masks (EN14683 certified).
Chinese Government Regulation Changes
This week’s regulation change brought in by the Chinese government is the requirement for customs to undertake an onsite inspection of the shipment before product can be released. This is to try and gain control of product leaving the country and clamp down on counterfeit items.
Whilst needed, this new regulation has caused a massive problem for suppliers as countless shipments that were already in the queue at customs will no longer be allowed through. This has created a headache for many companies as there is now not only the time required for customs to clear but now also the backlog of orders waiting to pass inspection.
Due to these delays, manufacturers are now pushing up their Minimum Order Quantities, making it unfeasible for some buyers to be able to purchase. One Point Zero is working on collating smaller orders into 1 large order internally and then distributing out the product once it has successfully landed in its destination country. This is allowing smaller organisations such as local councils to provide for their residents.
Why are is there less availability for gowns?
With masks being the primary concern in the last few months, gowns are now becoming the more urgent requirement, especially in the UK.
Generally, gowns are not as readily available to ship as masks for several reasons:
-
Weight- due to their size, boxes of gowns are heavy which makes them expensive to ship by air (the quickest form of transport for distribution). Companies are giving priority to masks as they can fit far more units onto a pallet than they can with gowns.
-
Production is slower than masks- with suppliers able to produce millions of masks a day, gowns take longer with the best factories producing a maximum of 100,000 gowns per day.
-
Raw materials- fabric procurement for gowns is in constant competition with masks as a factory can make more masks from a roll of material than gowns, making masks easier and more profitable.